How does a Warehouse Management System Help?
How does a WMS boost productivity, accuracy and reliability in my warehouse operations?
The 3 keys to how a WMS helps improve your warehouse operations
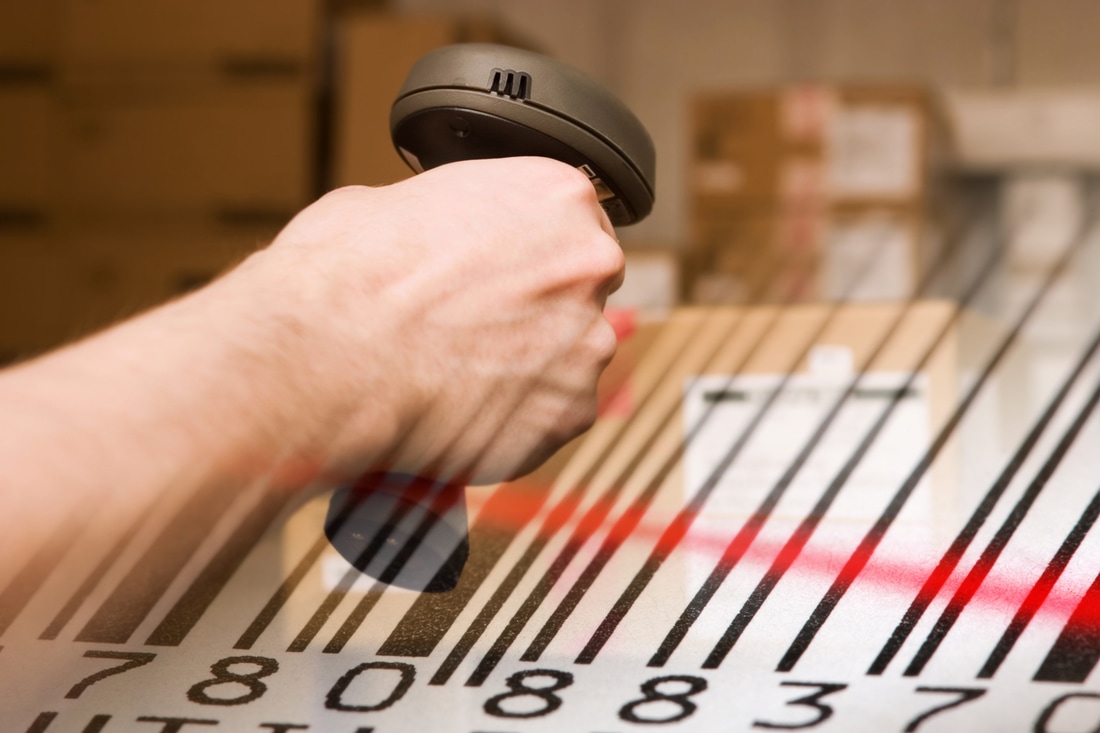
1. Accuracy
Fulfillment that fulfills
The key to warehouse accuracy is the ability to use id coding on the physical products, bin locations and load carriers (pallet, trolley, tub) to ensure system directed actions are completed accurately during the physical move.
Id coding is usually a barcode but could also be an RFID tag or a human readable code when voice technology is used.
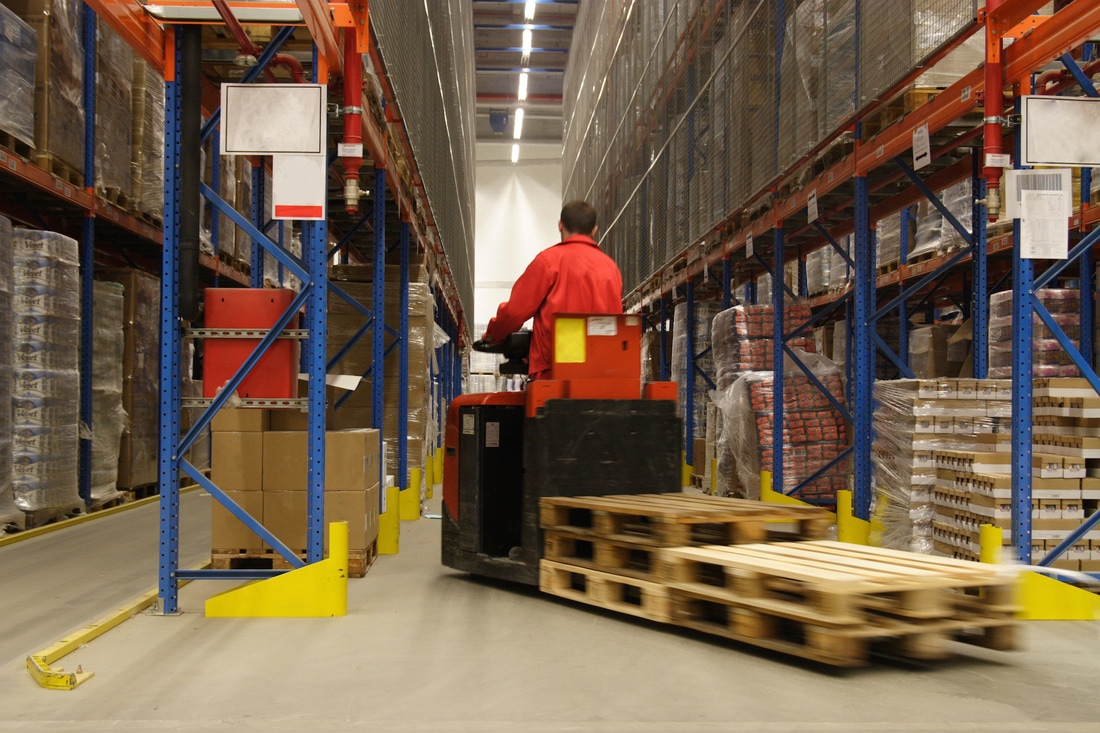
2. Productivity
A low cost warehouse
The key to warehouse productivity is the ability to use sophisticated algorithms to optimise warehouse tasks by minimising travel and combining tasks. The WMS uses static data about the warehouse and inventory, and real time dynamic data on product movements within the warehouse for its optimisation algorithms. This sophistication can only be done by the most advanced systems such as Upimium WMS.
Static data includes bin location capacity and layout, item dimensions and unit of measure configurations, materials handling equipment and the operational rules for the warehouse.
The operational rules control what items get stored where, what materials handling equipment can use them, which tasks operators can perform etc.
Dynamic data are put-away, replenishment, picking, counting, tasks with priorities assigned by the managers of the warehouse.
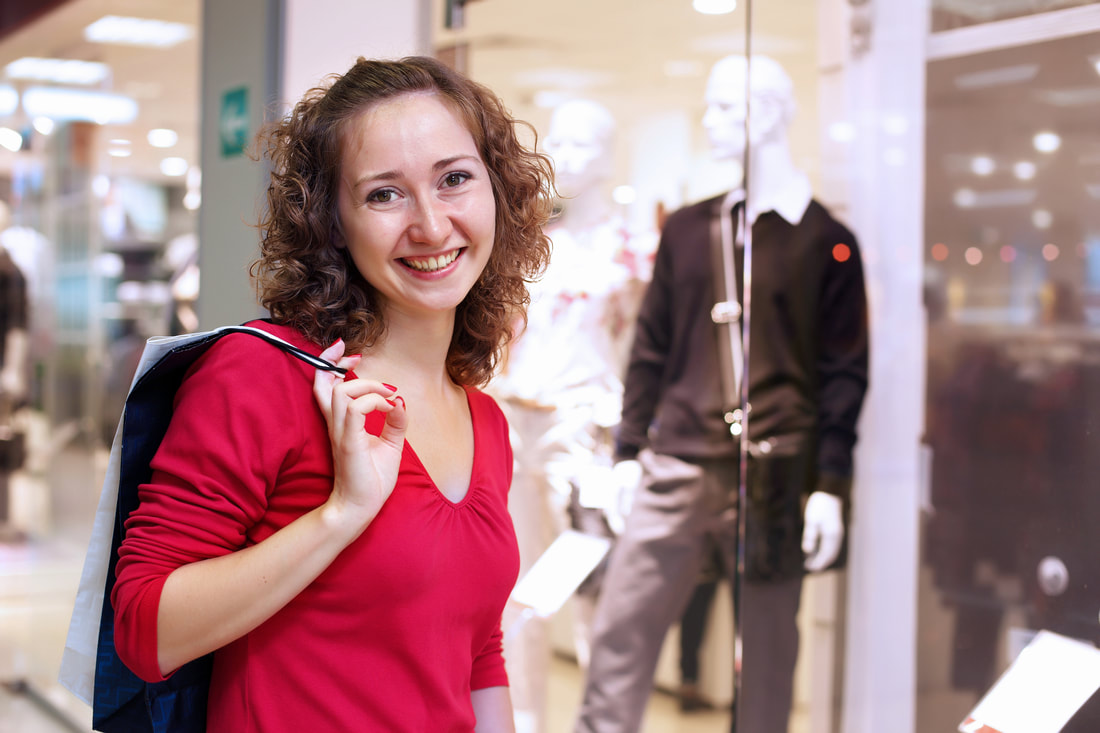
3. Reliability
A satisfied customer
The key to warehouse reliability – the ability to produce the same result repeatedly, is built in to the way a warehouse management system works. Warehouse operators are directed to do each task in the most efficient way possible every time. Id scanning during each task builds in accuracy at every step. All tasks to brought to completion and the status of all warehouse activity is monitored on a WMS dashboard.
This must be combined with good management practice and operational discipline to realise the full benefits.
What benefits does a Warehouse Management System (WMS) provide?
WMS Benefits by Warehouse Function
WMS Productivity: –
Receiving
A warehouse operator scans products from an inbound shipment and reconciles the delivery against an Advanced Shipping Notice (ASN) or Purchase Order as they unpack and sort the stock ready for put-away. Full pallets are scanned to confirm receipt and staged ready for immediate put-away. There is no subsequent admin task for PO/ASN receipt confirmation, it is done on the mobile scanner during the physical task. The PO/ASN receipt is interfaced to the business system either immediately or it may be delayed until the stock has been put-away and is available for sale.
WMS Productivity: –
Put-away
Stock is available for put-away immediately after physical receipt, which speeds the receipt to dispatch process. Stock on special order or back order is identified by the WMS for cross docking to eliminate a pick task. Put-away operators are directed by the WMS to an empty bin which eliminates searching. Stock storage is controlled by the WMS so that faster moving product is put to fast retrieval zones. Mixed item put-aways are directed in a logical travel path to minimise put-away travel distance.
WMS Productivity: –
Replenishment
Many business systems lack any ability to manage replenishment of pick faces and reserve stock is controlled manually (often in untracked bin locations). A WMS manages the replenishment of pick faces either on demand or in advance of picking tasks, so that overall stock movements for order picking are optimised.
WMS Productivity: –
Picking
WMS Productivity: –
Packing
WMS Productivity: –
Cycle-Counting
WMS Task Elimination: –
Eliminate Stocktake
WMS Visibility & Control: –
Warehouse-Manager
WMS Task Elimination: –
Warehouse-Admin
WMS Task Elimination: –
3PL Biling
WMS Flexibility: –
Fast Training of Casual Labour
WMS Cost-Reduction: –
Reduced Wear on Equipment
WMS Value-Improvement: –
Improved Customer Satisfaction
WMS Value-Improvment: –
Reduced Return
WMS Cost-Productivity: –
Increased Throughput Capacity
WMS Task-Elimination: –
Eliminate Paperwork
WMS Task-Elimination: –
Eliminate Data Entry
WMS Accuracy: –
Improved Inventory Accuracy
WMS Capacity: –
Improved space management
WMS Productivity: –
Reduced Search Time
WMS Productivity: –
Task Interleaving
WMS Accuracy: –
Rapid Error Correction
WMS Task_Elemination: –