If you want to run a profitable Third Party Logistics business you need a multi-client Warehouse Management System
If you want to compete effectively and scale up your 3PL, you need the best system available and the best implementation partner
Third party logistics service providers have unique needs that are not supported by simple accounting systems or even by the most advanced ERP systems. They need a multi-client warehouse management system with support for activity tracking, labour management and billing. They need to be able to provide clients with real time access to their inventory and activity or provide full integration of transactions with the client’s business system. This has become the standard expectation of most businesses that outsource their logistics to a 3PL. You may struggle to grow your business without a WMS and you will almost certainly not win any large accounts.
Manual Inventory Tracking is holding your 3PL business back from growth and profitability
Some 3PLs rely solely on manual tracking of their client’s inventory. As a consequence they struggle with low productivity and marginal profitability and are unable to provide reliable and timely information on activity and inventory to their clients.
Tracking Inventory in your ERP business system is Inadequate for a 3PL
Some 3PLs have implemented a conventional ERP system. This gives them inventory management but lacks support for:
- activity tracking,
- labour management,
- billing and
- client integration or
- client data access portal and
- is full of business accounting features that are completely irrelevant to their business.
As soon as you implement an ERP system for your 3PL you will have a data entry problem. How will you get your client orders into the system? This requires manual data entry or at very least a file upload solution (if you can get your clients to send you orders in an Excel file). You ideally need to integrate with your clients in some way to automate data exchange, many traditional ERPs (yours or your clients’) are not built to do this easily.
Developing your own WMS leads to an expensive dead end
Some 3PLs develop their own warehouse management system but their solution lacks breadth of experience in both software development and logistics. Their in house solution grows into a compromised monster over time and lacks functionality and flexibility and may also be plagued with issues and bugs as more and more code gets tacked onto a fundamentally flawed base.
Grow your business profitably with a Warehouse Management System designed for 3PL
Warehouse Management Systems typically improve productivity by up to 30% (depending on current circumstance) with payback periods of 6-18 months. The larger the staffing, the more basic the current systems the shorter the payback period.
The productivity gains from a WMS will be achieved in the following areas:
- The elimination of administration data entry tasks related to inbound and outbound order entry, receiving and shipping confirmations and activity tracking for billing. If you’re using an ERP to run your operations, this could the single biggest contributor to productivity gain across the business.
- Elimination of manual stock counts for client reporting.
- Streamlined receiving and put-away processing that operates in a flow process rather than delivery based sorting and checking.
- Reduction of picking time due to bin location management.
- Reduction of travel path from more efficient product slotting due to improved management capability of pick faces, replenishment and directed storage.
- Reduction of travel path through implementation of advanced multi-order picking methods.
- Product pictures on mobile device aid product identification.
- Better control with directed staging of outbound orders.
- Automation of the delivery run sheets and manifests.
- Integration with a freight management system with order picking or packing to eliminate manual consignment note entry.
- Pre-consigning of outbound orders to apply freight labels during picking.
Other benefits that will also reduce cost include:
- Barcode scanning and real time transaction control leads to:
- improved inventory accuracy and less stock outs due to missing stock,
- less picking errors, reduced returns and credits, enhanced reputation.
- Directed put-away reduces lead times for put-away and order fulfillment.
- Traditional paper based administrative tasks for purchase order receiving and sales order confirmation are eliminated making host system tracking of activity more timely and reducing administrative overhead.
- General productivity boost increases the throughput capacity of warehouse enabling you to ship more from the same space.
- Easy to learn step by step transaction workflow makes most warehouse tasks quick to learn, shortening the time from hiring to effectiveness for casual labour. Also providing more flexibility to manage peak workloads with additional staff.
- Tracking log of every mobile device action feeds into a labour management system so that standard activity costs can be developed. This helps with cost control and labour management.
- The activity tracking data is also used to price billable activities in 3PL. Priced activity data can then be extracted to an accounting system for client invoicing and reporting.
- Online access for clients to see their own data and produce reports and downloads will reduce the need for customer service calls and demands for manual stock counting or reporting and data extract.
Upimium Warehouse Management Suite is the warehouse management system you’ve been looking for to run your 3PL
Upimium WMS has been built on innovative 21st century software architecture. Upimium WMS was built specifically to provide rapid, non-programmatic customisation for client workflow that puts you in control of your system without the need for slow and expensive customisations by the developer every time you get a new requirement from a client.
You can innovate fast, keep your clients and their customers happy, and scale your business profitably and without stress.
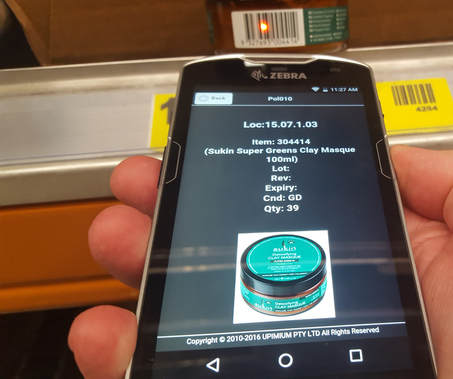
Logistics Help are the implementation partners for Upimium. We are bringing the critically important technology of modern and innovative WMS to small and medium Third Party Logistics businesses that have gone without a system or have implemented compromised solutions.
Upimium is an Australian supply chain software company with its origins in consulting and implementation of large scale WMS solutions using HighJump. Upimium is born of great experience and innovative thinking.